The Ultimate Guide to AC DC TIG Welder
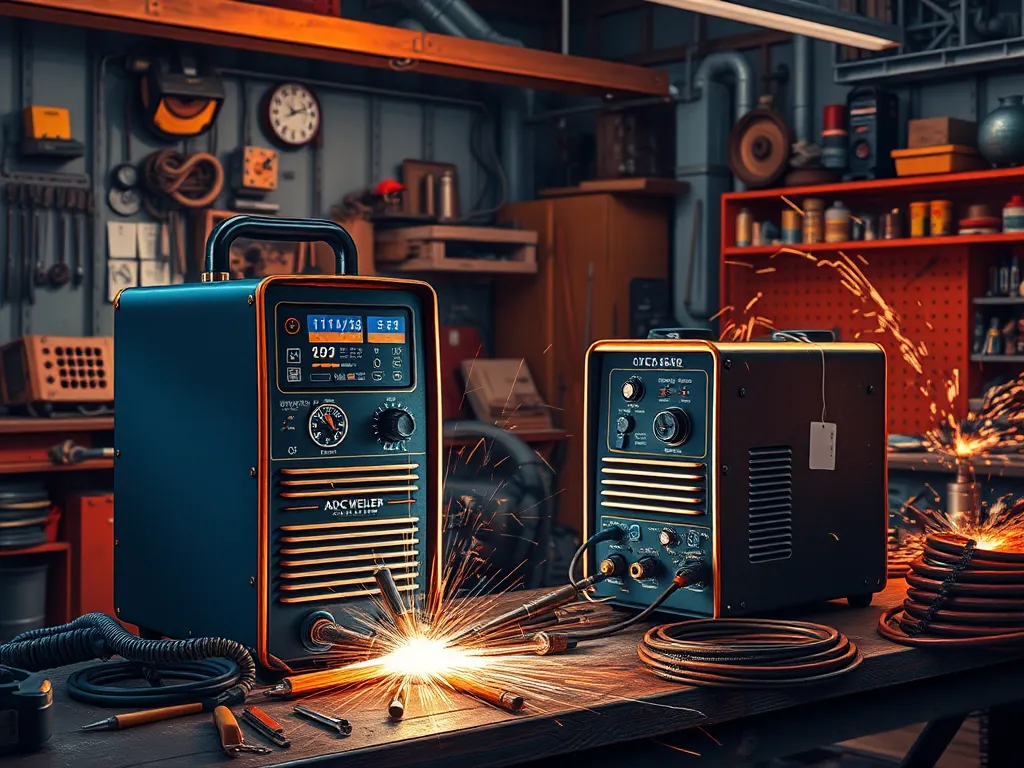
The Ultimate Guide to AC DC TIG Welder
AC DC TIG welder is a versatile welding machine that is designed to provide precision and control in various welding applications. Whether you’re working on automotive repairs, custom metal fabrication, or artistic welding, an AC DC TIG welder can meet your needs. In this guide, we will explore the features, advantages, applications, and maintenance of AC DC TIG welders.
If you're planning to get a new AC DC TIG welder , you'll want to get the best one on the market. Luckily for you, we've got some insights for you. Check out Mohamed I Qoquf's article on why the AC DC TIG welder might be the perfect tool for your needs.
Before we dive into the details, let's first understand what an AC DC TIG welder is. An AC DC TIG welder is a type of welding machine that utilizes a tungsten electrode to create an electric arc for welding. It can be used to weld both ferrous and non-ferrous metals, making it suitable for a wide range of applications.
So, how does an AC DC TIG welder work? The welding process involves creating a high-frequency electric arc between the tungsten electrode and the workpiece. The electric arc generates heat, which melts the metal and forms a weld joint. The welder also provides variable amperage control, allowing you to adjust the heat output based on the thickness and type of metal being welded.
One of the key features of AC DC TIG welders is high-frequency start. This feature enables the welder to start the arc without direct contact between the electrode and the workpiece. High-frequency start ensures a clean and precise arc, reducing the risk of electrode contamination and enhancing the quality of the weld.
Another notable feature of AC DC TIG welders is pulse welding. Pulse welding allows for better control of the heat input, minimizes distortion, and improves weld quality. By pulsing the current, you can maintain a lower average heat input while still providing sufficient penetration and fusion.
Overview
An AC DC TIG welder is a versatile welding machine that can be used for various applications. It provides precision and control, making it ideal for welding intricate or delicate joints. The ability to adjust the heat output and pulse the current allows for precise control over the welding process.
The welding process of an AC DC TIG welder involves creating an electric arc between the tungsten electrode and the workpiece. The arc generates heat, which melts the metal and forms a weld joint. The welder provides variable amperage control, allowing for precise adjustment of the heat output. This makes it suitable for welding different thicknesses and types of metal.
Features
High-frequency start is a key feature of AC DC TIG welders. It enables the welder to start the arc without direct contact between the electrode and the workpiece. This ensures a clean and precise arc, reducing the risk of electrode contamination and improving weld quality.
When it comes to welding, having the right tools, specifically an AC DC TIG welder , is crucial for a smooth operation. If you're still undecided, we recommend you consider our top pick. Explore this guide for a detailed review of the best welders for beginners.
Pulse welding is another important feature of AC DC TIG welders. It allows for better control of the heat input, minimizing distortion and improving weld quality. By pulsing the current, you can maintain a lower average heat input while still achieving sufficient penetration and fusion.
Variable amperage control is a feature that allows for precise adjustment of the heat output. This is essential when welding different thicknesses and types of metal. Being able to control the amperage ensures that the weld has the appropriate heat input for a strong and reliable bond.
Foot pedal control is a convenient feature that allows for hands-free operation of the welder. By using a foot pedal, you can easily adjust the amperage while keeping your hands on the workpiece. This provides a seamless welding experience and enhances precision.
Advantages
One of the advantages of using an AC DC TIG welder is its ability to weld both ferrous and non-ferrous metals. Whether you're working with stainless steel, aluminum, or copper, an AC DC TIG welder can handle the job. This versatility makes it a valuable tool for various industries.
Precision and control are other key advantages of AC DC TIG welding. The ability to adjust the heat output and pulse the current allows for precise control over the welding process. This is particularly important when welding intricate or delicate joints.
When it comes to aesthetics, AC DC TIG welding produces clean and aesthetic welds. The precise control over the heat input and the use of a non-consumable tungsten electrode result in a weld with minimal spatter and a smooth appearance. This is important for applications that require an aesthetically pleasing finish.
Better heat control is another advantage of AC DC TIG welding. The ability to adjust the amperage allows for precise control over the heat input, minimizing the risk of overheating or underheating. This is especially important when working with heat-sensitive materials.
Applications
AC DC TIG welders have a wide range of applications in various industries. One common application is automotive repairs. Whether you're repairing body panels or exhaust systems, an AC DC TIG welder can provide the precision and control needed for a strong and durable repair.
Are you in need of an AC DC TIG welder for your welding projects? Don't delay your projects; take action today. Get started by sieving through expert advice in this comprehensive welding guide . Don't compromise on your welding needs; select the best!
Custom metal fabrication is another area where AC DC TIG welders excel. From creating intricate metal artwork to fabricating custom parts, AC DC TIG welding allows for precise and clean welds. The versatility of the welder also makes it suitable for welding different types of metal.
Improve your craft with high-quality AC DC TIG welding equipment. If you’re on the fence about where to get started, we’ve got you covered. Delve into this beginner's guide and see why AC DC TIG welders command respect in the welding industry.
Pipe welding is another important application of AC DC TIG welding. The ability to control the heat input and produce clean welds makes AC DC TIG welders ideal for welding pipes. Whether you're working with stainless steel, carbon steel, or other materials, an AC DC TIG welder can deliver quality results.
The AC DC TIG welder —a game-changer in metallurgy. With its powerful AC/DC functionality, it delivers efficiency that few tools can match. As welding professionals, we highly recommend it. Learn why by reading this insightful article - a must-read for anyone considering an AC DC TIG welder.
The aerospace industry also benefits from the precision and control of AC DC TIG welding. From aircraft structural welding to welding delicate components, AC DC TIG welders provide the necessary precision and control for aerospace welding applications.
In addition to industrial applications, AC DC TIG welding is also widely used in artistic welding. The ability to create clean and aesthetic welds makes it a preferred choice for artists who work with metal. AC DC TIG welders allow artists to bring their creative visions to life.
Maintenance
Proper maintenance is essential to ensure the longevity and performance of your AC DC TIG welder. Regular cleaning and inspection of the welder and its components help prevent issues and ensure optimal performance.
Electrode and tungsten replacement is another important aspect of maintenance. Regularly checking and replacing worn-out electrodes and tungsten is necessary to maintain weld quality and prevent electrode contamination.
Managing the gas and coolant is crucial for AC DC TIG welders. Checking the gas and coolant levels and ensuring proper flow is important for maintaining optimal welding conditions and preventing overheating.
Component replacement and repair may be necessary over time. It's important to have a qualified technician inspect and repair any faulty components of your AC DC TIG welder to ensure safe and efficient operation.